Specialist Guidance on What is Porosity in Welding and Just How to Address It
Specialist Guidance on What is Porosity in Welding and Just How to Address It
Blog Article
The Scientific Research Behind Porosity: A Comprehensive Guide for Welders and Fabricators
Understanding the elaborate systems behind porosity in welding is essential for welders and producers making every effort for impressive craftsmanship. From the make-up of the base materials to the ins and outs of the welding process itself, a multitude of variables conspire to either exacerbate or alleviate the existence of porosity.
Understanding Porosity in Welding
FIRST SENTENCE:
Assessment of porosity in welding discloses vital insights into the integrity and high quality of the weld joint. Porosity, identified by the existence of cavities or gaps within the weld metal, is a common problem in welding processes. These spaces, otherwise properly attended to, can endanger the structural stability and mechanical residential or commercial properties of the weld, causing possible failings in the ended up product.
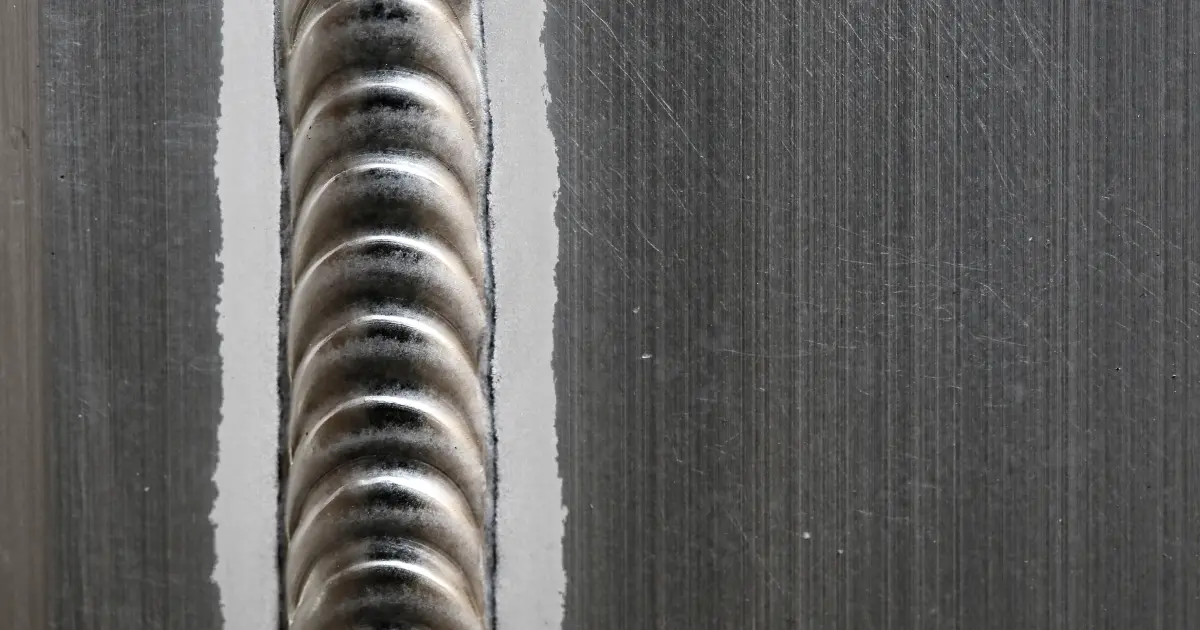
To identify and evaluate porosity, non-destructive screening techniques such as ultrasonic testing or X-ray evaluation are frequently utilized. These methods enable the recognition of interior defects without endangering the stability of the weld. By analyzing the dimension, shape, and circulation of porosity within a weld, welders can make educated decisions to boost their welding processes and attain sounder weld joints.
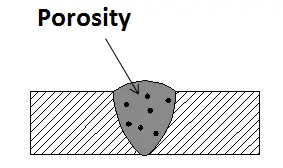
Elements Affecting Porosity Formation
The incident of porosity in welding is influenced by a myriad of variables, ranging from gas protecting performance to the ins and outs of welding parameter settings. Welding specifications, consisting of voltage, current, take a trip speed, and electrode kind, additionally effect porosity development. The welding strategy utilized, such as gas metal arc welding (GMAW) or protected metal arc welding (SMAW), can affect porosity development due to variants in warm distribution and gas coverage - What is Porosity.
Impacts of Porosity on Weld Top Quality
Porosity development substantially endangers the architectural honesty and mechanical residential or commercial properties of welded joints. When porosity is present in a weld, it develops voids or tooth cavities within the material, decreasing the general toughness of the joint. These spaces serve as anxiety focus factors, making the weld extra vulnerable to splitting and failing under load. The visibility of porosity also deteriorates the weld's resistance to deterioration, as the trapped air or gases within deep spaces can respond with the surrounding atmosphere, leading to destruction over time. Additionally, porosity can prevent the weld's capacity to withstand Extra resources pressure or effect, further endangering the general quality and reliability of the bonded framework. In important applications such as aerospace, automotive, or architectural building and constructions, where safety and resilience are critical, the damaging impacts of porosity on weld high quality can have serious consequences, highlighting the relevance of minimizing porosity go to my blog through appropriate welding techniques and treatments.
Techniques to Lessen Porosity
Additionally, making use of the appropriate welding specifications, such as the correct voltage, current, and take a trip rate, is vital in preventing porosity. Keeping a constant arc size and angle during welding also assists minimize the possibility of porosity.

Using the ideal welding strategy, such as back-stepping or employing a weaving movement, can additionally assist disperse heat uniformly and decrease the chances of porosity development. By applying these strategies, welders can successfully lessen porosity and generate high-quality welded joints.
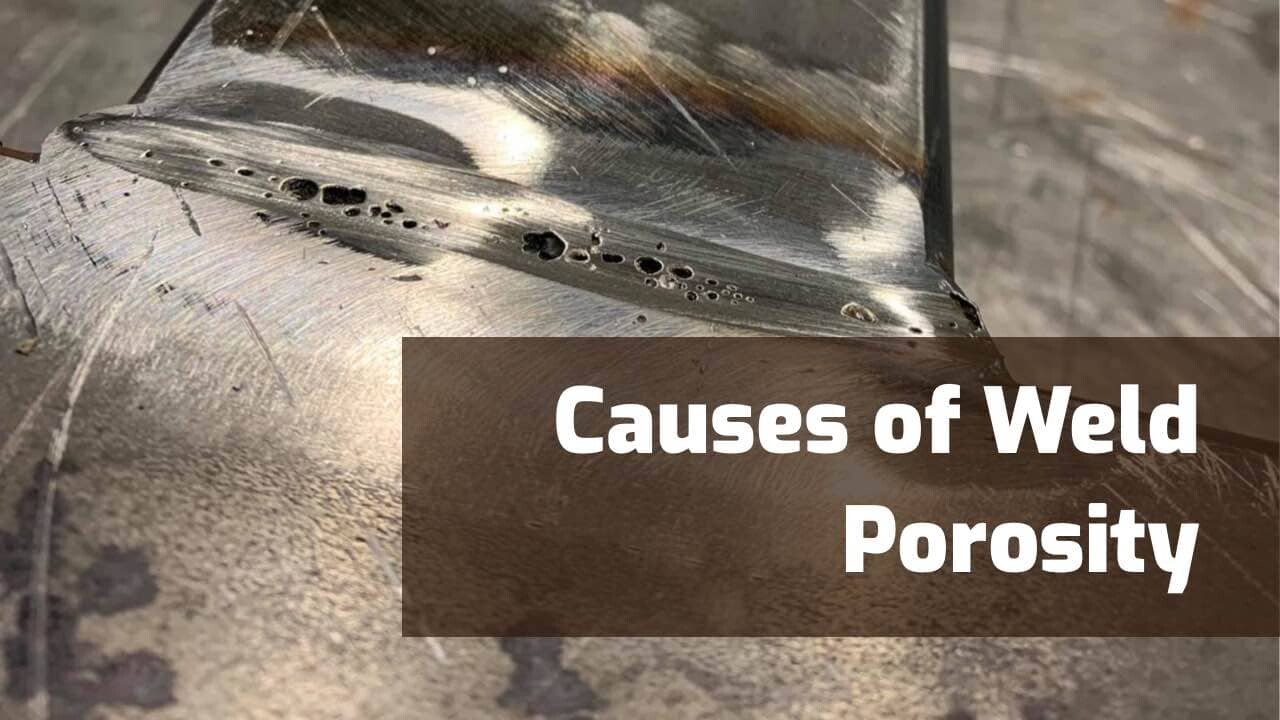
Advanced Solutions for Porosity Control
Implementing innovative technologies and ingenious methods plays a crucial function in accomplishing remarkable look at these guys control over porosity in welding procedures. In addition, employing innovative welding strategies such as pulsed MIG welding or modified atmosphere welding can likewise assist reduce porosity concerns.
Another sophisticated solution entails the usage of advanced welding tools. Making use of tools with built-in attributes like waveform control and innovative power resources can enhance weld quality and decrease porosity threats. In addition, the application of automated welding systems with precise control over specifications can considerably minimize porosity defects.
Additionally, integrating innovative tracking and assessment modern technologies such as real-time X-ray imaging or automated ultrasonic screening can aid in detecting porosity early in the welding procedure, enabling instant corrective actions. On the whole, incorporating these innovative remedies can considerably boost porosity control and boost the total top quality of welded elements.
Conclusion
In final thought, comprehending the scientific research behind porosity in welding is essential for welders and producers to generate premium welds - What is Porosity. Advanced solutions for porosity control can even more boost the welding procedure and guarantee a strong and reputable weld.
Report this page